Summary of metal 3D printing process.
작성자
MERAIN
작성일
21-11-08 14:35
조회수
1,995
본문
- Summary of metal 3D printing process (METALAM PROCESS)
The criteria for writing were based on the PBF method.
Metal 3D printing is a process in which the laser splits one by one through a process called slicing based on 3D data and stacks the pictures corresponding to one layer along the hatching path and repeatedly applying powder. The figure below shows a schematic diagram of the entire metal 3D printing process.
The form of powder, which is mainly used in the PBF metal printing method, is made into a spherical form, and there are various reasons, such as densification of powder and liquidity flow.
The common part of all metal 3D printing processes is heat treatment and post-processing. In metal 3D printing, heat treatment and post-processing are more important than printing. And filtering for reusing metal powder (Sieving - the process of removing impurities to obtain complete metal powder) and reorganizing equipment (filter replacement, laser lens cleaning, etc.).
In the case of post-processing, it varies depending on the purpose and use material, so you must check it before manufacturing it with metal AM. For products made of metal AM, the flow of the entire process from product design to post-printing is important.
- What would be good for metal 3D printing?
The reason for 3D printing is optimized for prototype production and customized multi-species production. Since the manufacturing method of the powder material is expensive, the output cost is also expensive. Therefore, it is mainly used in special fields such as medical, aviation, automobiles, molds, and materials, which are high value-added industries. Metal 3D printing is like welcome rain in this special field.
There are about three reasons for metal 3D printing.
The first is the degree of freedom in design. There is no need to think about areas that cannot be processed when designing. Cutting processing, which contrasts with stacking processing, is a processing method that cuts iron by attaching an end mill to a motor and rotating it at high speed, but complicated parts (undercuts) inside the shape cannot be processed. However, additive processing is very free to design because there is no shape restriction, and any shape can be made with only a supporter attached. You can make it in the shape you want. You can understand it as the concept of shaving and stacking.
NC : I'm cutting it. 3D Printer : Additive
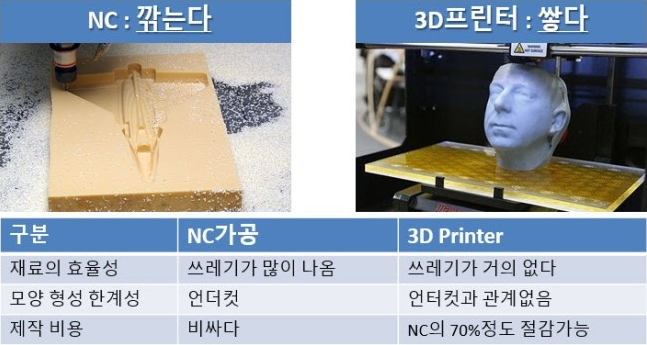
When iron is cut, pieces (waste) called chips come out. On the other hand, the chip does not occur because it only forms the necessary parts.
The second reason is lightening. Since you can freely shape the product, you can remove unnecessary parts and print only the necessary parts. Lightening is feasible through grid structure and phase optimization and can be used in a combination of two. Grid structure refers to replacing unnecessary parts with grid structures, and phase optimization is a concept that optimizes the structure of objects and optimizes material distribution within a given design space. When proceeding with lattice structure and phase optimization, it is necessary to reduce weight while meeting the performance goals (strength, dimensions, performance) of the designed product.
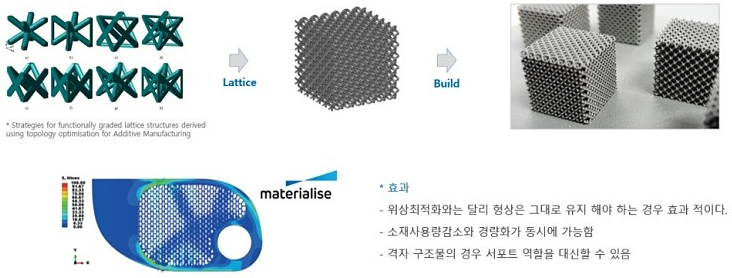
[Picture] The process of lattice structure and lightening effect - Materialise
There are also various programs that can simulate this lamination process. Since it is a structural analysis area, most of them will be developed by companies that develop analysis SW. The grid structure serves as a support (support) at the same time as it is lightweight, and the application of lightweight is very useful in various fields. For example, in the case of drones, lightening parts reduces weight and consumes less engine, which means longer body time.

[Picture Altair Optimization - Inspire]

[Picture] Stacked manufacturing simulation SW - ANSYS, Materialise, and Authalk.
The third reason is customized multi-breed production.That's what it is. When manufacturing teeth and bone implants that fit the patient's body, it can be customized for the patient by bringing in the patient's medical scan data, and weight can be reduced through weight reduction. It also helps to improve durability because it is possible to directly print products made by assembling multiple parts into a single product state.
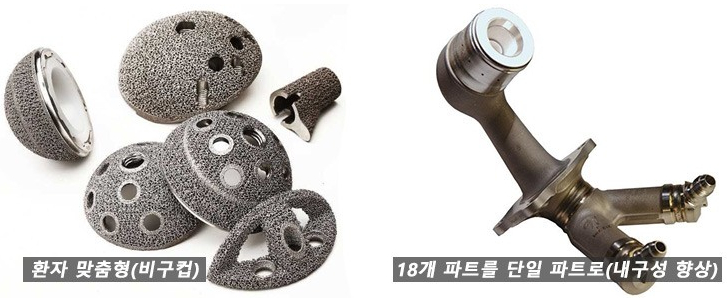
[Picture] Acam non-ball cup sample, right) Ge Aviation engine nozzle.
I briefly wrote down the entire process of metal 3D printing and why it is necessary.
Thank you.
- 다음글DfAM(Design for Additive Manufacturing) 21.11.08